Thinking about Design Requirements
In this book, we will walk through four custom 3D printing projects in Blender. First, we will use Bezier curves to make a custom shape, the silhouette of a child, for a profile pendant. Our second project, a coordinate bracelet, illustrates building with standard shapes and how text can be used to personalize models. You'll get more acquainted with mesh modeling tools and Boolean intersections in our third project, creating a textured house figurine. Finally, you'll learn how Blender can be used for organic shapes as you work on modeling a human hand.
Before you build a house, before you sew a quilt, the process begins with a plan. The same is true with 3D modeling and 3D printing. When you model with your design requirements in mind, every measurement, every angle, every click of the mouse, all work toward your end goal. This chapter will cover some key questions to reflect on before you begin to model:
- What type of printing process will be used to make your design?
- How does that process impact design elements such overhangs, detailing, and wall thicknesses?
- How big do you want the final piece to be?
Thinking about printing processes
Not all 3D printers work in the same manner. The printers at the Service Bureaus, such as Shapeways, Sculpteo, and iMaterialise, use different types of technology than what is typically seen with at-home desktop printers.
All 3D printers will start with your 3D model and use an additional piece of software called a slicer to cut your object up into small cross sections, or layers. From there, all the printing processes will create your object one layer at a time. Different types of printing, however, add the material in different manners. Those differences in production processes can impact how you approach your design.
Home printing – Fused Filament Fabrication (FFF) printers
Currently, the most common printers you would find in a home, library, makerspace, or neighborhood 3D Hub are what are called the Fused Filament Fabrication (FFF) or Fused Deposition Modeling (FDM) printers. I often describe these printers as similar to the hot glue guns you would see used for crafting or electronics projects. A spool of plastic string (filament) is fed through a hot end that heats the plastic up to the point where it is malleable and the printer can draw with it. The printer will print one layer of your object directly on a platform called the built plate, move up, print the next layer, and so on until your piece is finished.
Overhangs
With the exception of the Made in Space printer on the International Space Station, FFF/FDM printers are subject to gravity. Higher portions of your model will need a foundation or support from the lower ones. As a design consideration, you'll want to be conscious of the slopes in your piece, the overhangs. The angle of those overhangs impact how far a layer extends over the previous layer one. If a layer extends out too far, the filament could droop or curl up, causing imperfections, or worse, a failed print.
For most FFF/FDM desktop printers, the rule of thumb is 45 degree overhangs. If you keep your slopes and curves to 45 degrees or less, each layer will have a good foundation with the layer underneath. When you look at larger angles, you can see how layers may have trouble supporting their own weight. The following image shows the difference between 45 degrees and the more troublesome 85 degrees:
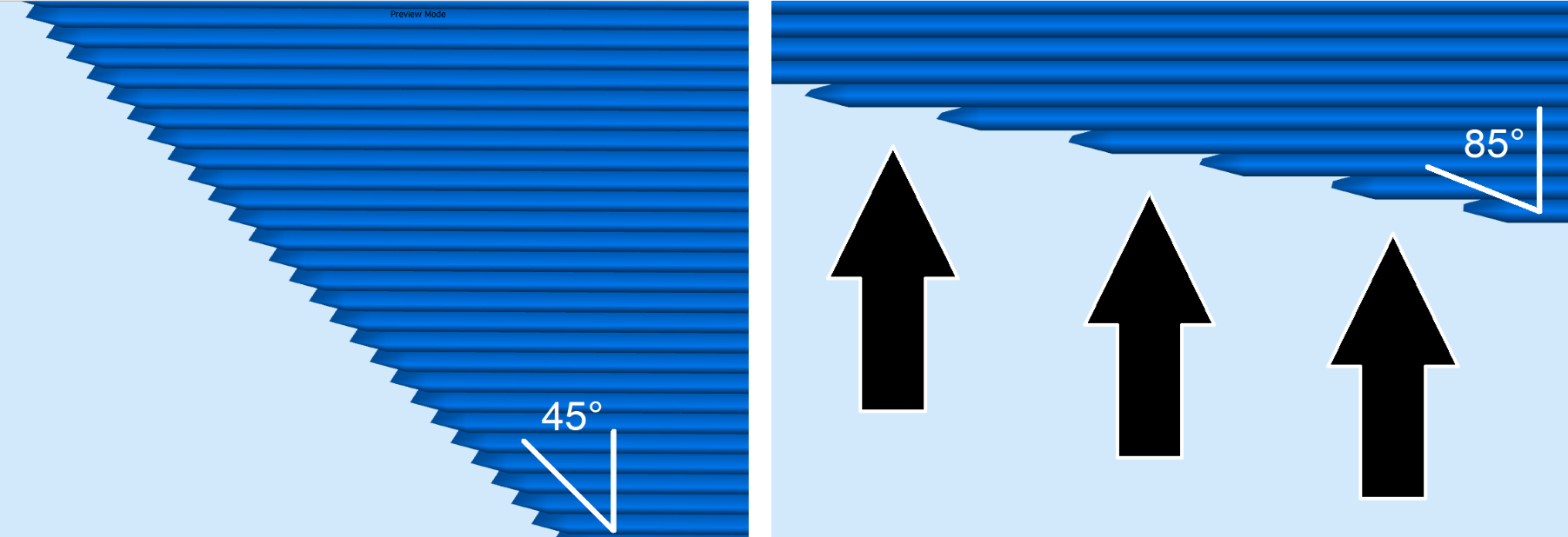
The human hand model later in the book is one where thinking about overhangs will be important. If one of the fingers was angled more than 45 degrees, you can see in the slicer preview how the printer would be drawing lines with nothing underneath it. For other portions of the finger that are more upright, you would see that each layer has good contact with the layer underneath:
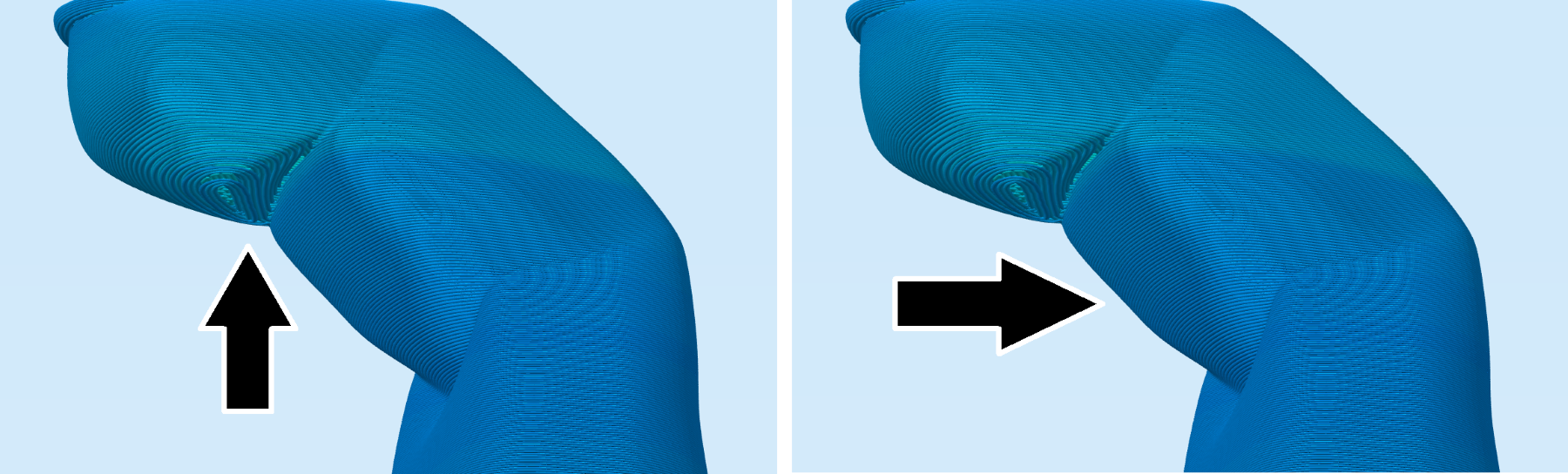
If you want to put your particular printer to the test and get an assessment of its overhang capabilities, try the Massive Overhang Test by thingster on Thingiverse at https://www.thingiverse.com/thing:40382.
There is a lucky exception with overhangs. When the printer starts a layer, it usually starts by printing perimeters, sometimes called outlines, of your object before filling in the inside. The molten plastic likes to stick to itself. That is exactly why FFF/FDM printing works. If your printer draws its outlines from the inside of your object to the outside of your object, the last outline, the part of your object that is visible, sticks enough to the earlier outlines that it can support its own weight. That gives the printer the ability to do small, unsupported 90 degree (completely horizontal) overhangs, a handy behavior for detailing of your model, giving it texture or personalization:
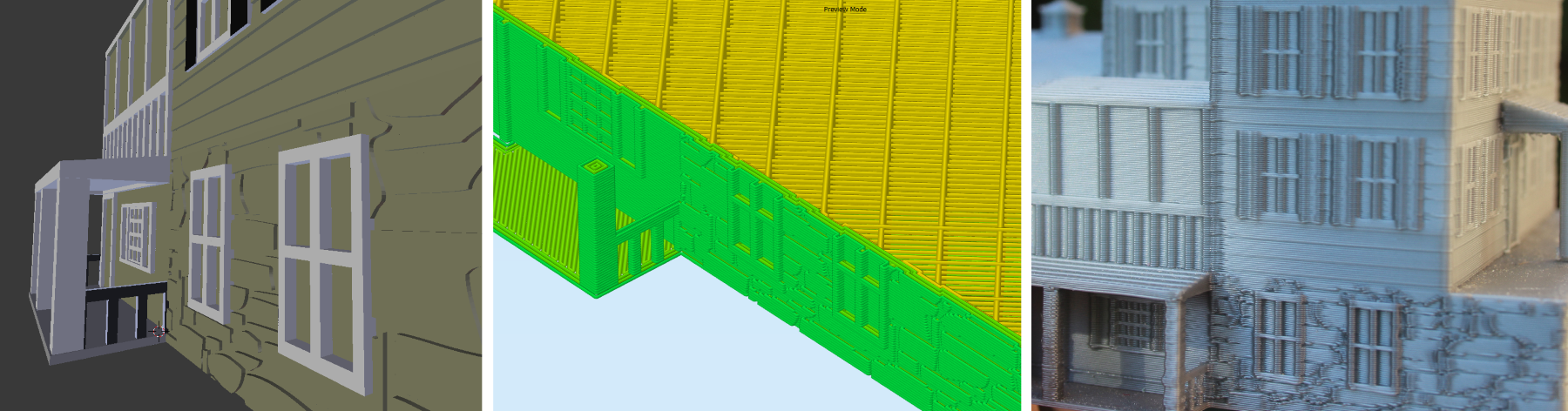
How far can those details come off a vertical face of the print? It will depend on the nozzle size of the printer. I have found 0.5mm to work great with both 0.35 and 0.4mm nozzles.
If you want to get an idea of what kind of unsupported details you can achieve on your printer, the Vertical Embossed Detailing - Remix by SpikeUK on Thingiverse is a good print to get an assessment: https://www.thingiverse.com/thing:2462735.
If you do have a design that requires large overhangs, you do not have to necessarily despair and abandon the idea. The slicer can tell the printer to print some extra columns called supports to assist your object. This is extra work for the printer that will add to your material usage and printing time. In addition, supports can leave markings on your piece, requiring sanding and cleanup to be done afterward. You don't have to avoid large overhangs when modeling, but it makes the printing process a lot cleaner if you do:
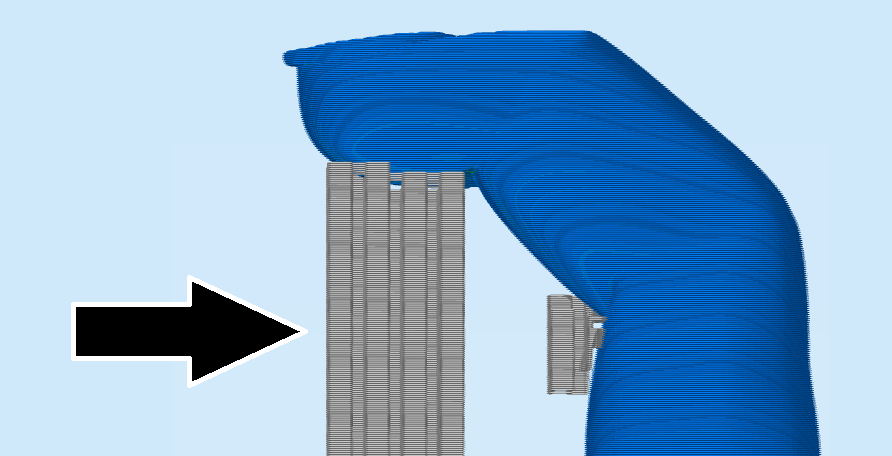
Detailing
If you were to crochet with thin embroidery floss, you could achieve a much more intricate level of detail than if you were working with thick yarn. The width of the thread being used plays a key role in what can be achieved in the final product. You can think of FFF/FDM printing as also using a thread, a small thread of plastic. With FFF/FDM printing, there are two dimensions of that thread that impact our detailing.
Layer height
When the slicer is cutting up your file into small cross-sections for 3D printing, the height of those cross sections is called the layer height. This can not only vary from printer to printer, but it can also vary from print to print. A smaller layer height would cut your model up into more cross sections. It would be a longer printing process, but at the same time would give your object a greater level of detail and resolution. In my prints, the layer heights tend to be between 0.10mm-0.25mm layers.
The following image shows the same piece with three different layer heights. As the layer height increases, the level of detail decreases:
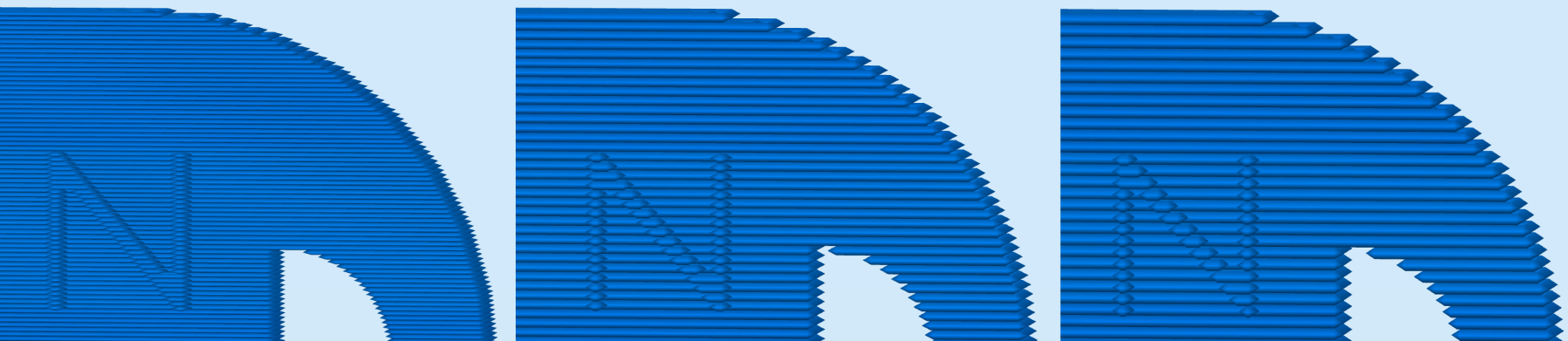
Thinking ahead about layer height is a worthwhile venture when embarking on a 3D modeling project, particularly if you are planning small detailing. Consider the house figurine that will be highlighted later in the book. If the window panes are shorter than the planned layer height, the slicer (and therefore the printer) will skip that detailing, as shown in the following image:
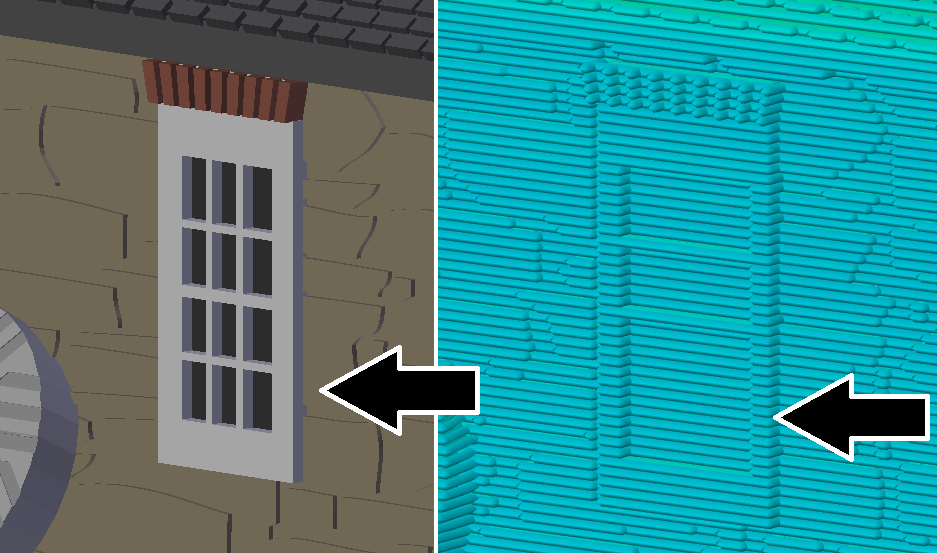
Extrusion width
As your printer lays down lines of malleable plastic to bring your model to life, the hole in the nozzle impacts how wide those lines are. You can also think of it as your thread width, how wide the thread of plastic that comes out of your nozzle is. A more technical term is extrusion width, how wide the extruded plastic is. That width isn't necessarily equal to your nozzle size. For example, a nozzle with a 0.4mm hole may be using a 0.42mm extrusion width.
You may be able to look up your extrusion width in your slicing software. Different slicers use different terminology. Three examples are:
Slicer | Setting |
Simplify3D | Extrusion Width |
Cura | Line Width |
Slic3r | Extrusion Width |
Extrusion width is important to consider during design as it can also impact the detailing of your piece, which is most readily visible on the top. Later in the book, we will create a bracelet with custom coordinates on the top. If that piece was printed flat on the bed and portions of text were thinner than the extrusion width (such as part of the number 4 in the following image), that detail could very well get skipped:
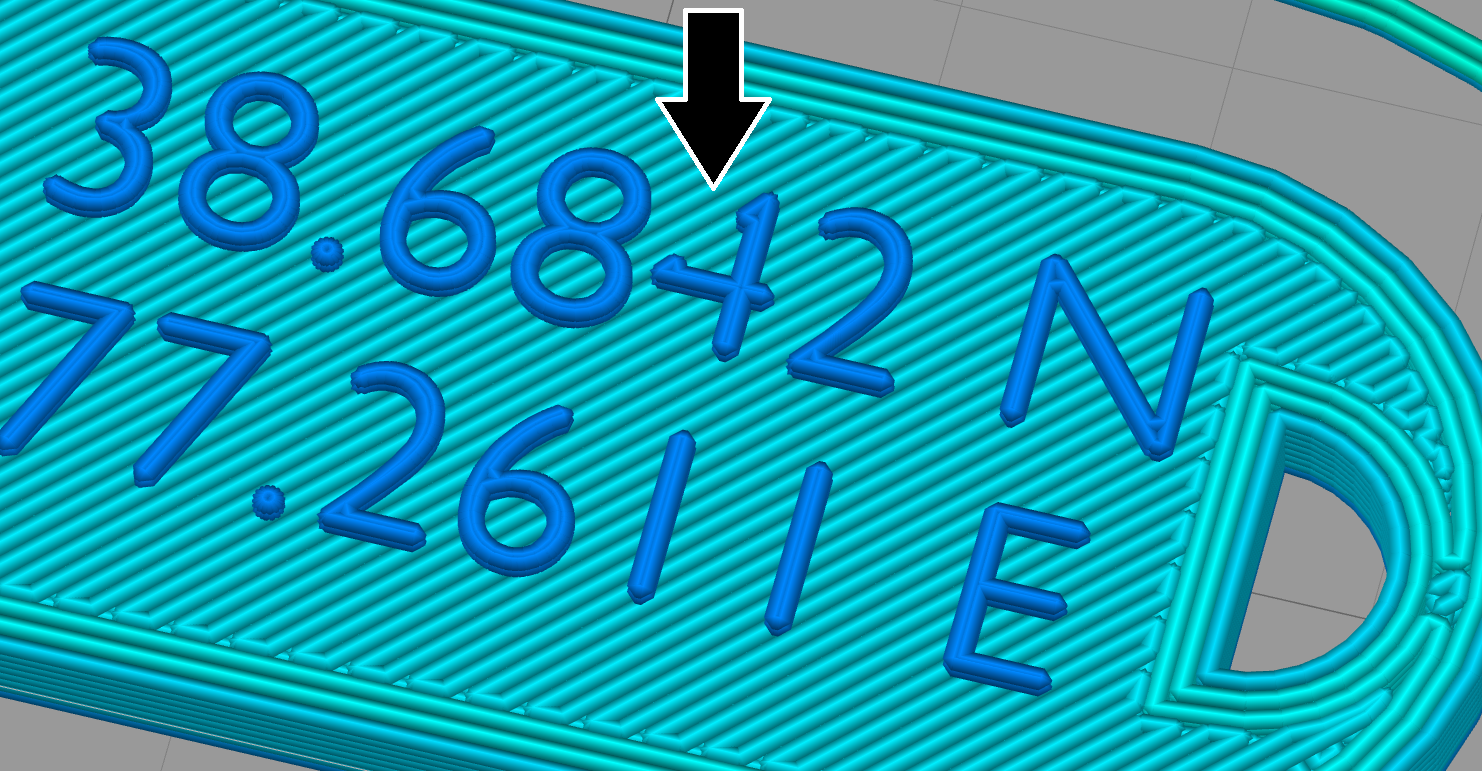
Layer heights are smaller, sometimes substantially so, than extrusion widths. That means detailing going up vertically can be finer than the horizontal details you have at the top. If we printed that coordinate bracelet on its side, the same number we had trouble with before shows up fine:
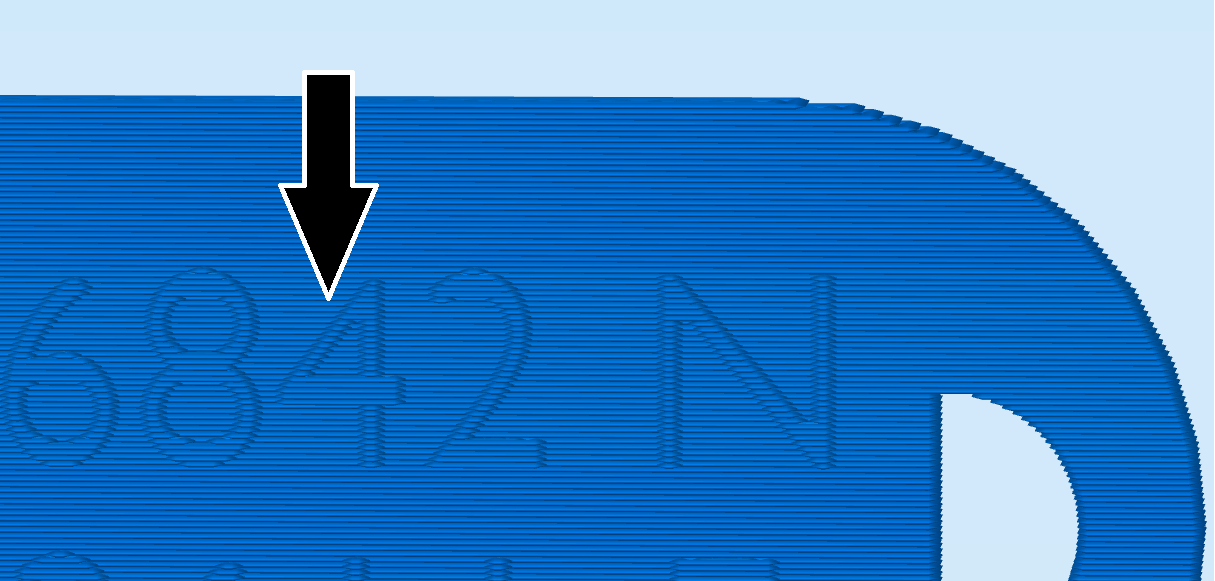
Wall thickness
Wall thickness is simply how thick your printed object is from side to side. Wall thickness directly applies to the strength of that section of the piece. Technically, you could have walls as thin as your extrusion width. You could have your printer print a single line of plastic thread for your entire piece and there are many examples of beautiful vases printed in that manner.
Depending on your application, that may not be the best plan of attack. A thin wall of 0.42mm is easy to break. Our first model in this book is a pendant based on the profile of one of my sons. This is a sentimental piece. Surely, I would not want the clasp to break during my daily activities. I would want to give the hook for the pendant enough strength to survive the wear and tear of my daily life. On the other hand, railing detailing on a house figurine would be purely decorative and not be subject to the same stress. I could go smaller there.
Another thing to consider is how this section of your print is attached to the rest of the model. If it is a wall connected to other sections on two or more sides, it is considered a supported wall. It does not have to have to be as thick as a wall that stands by itself, an unsupported wall. The front wall of a house figurine is an example of a supported wall. It is attached to many other sides, the left side of the house, the right side of the house, the roofing. On the other hand, the thickness of a profile pendant, I would consider an unsupported wall:
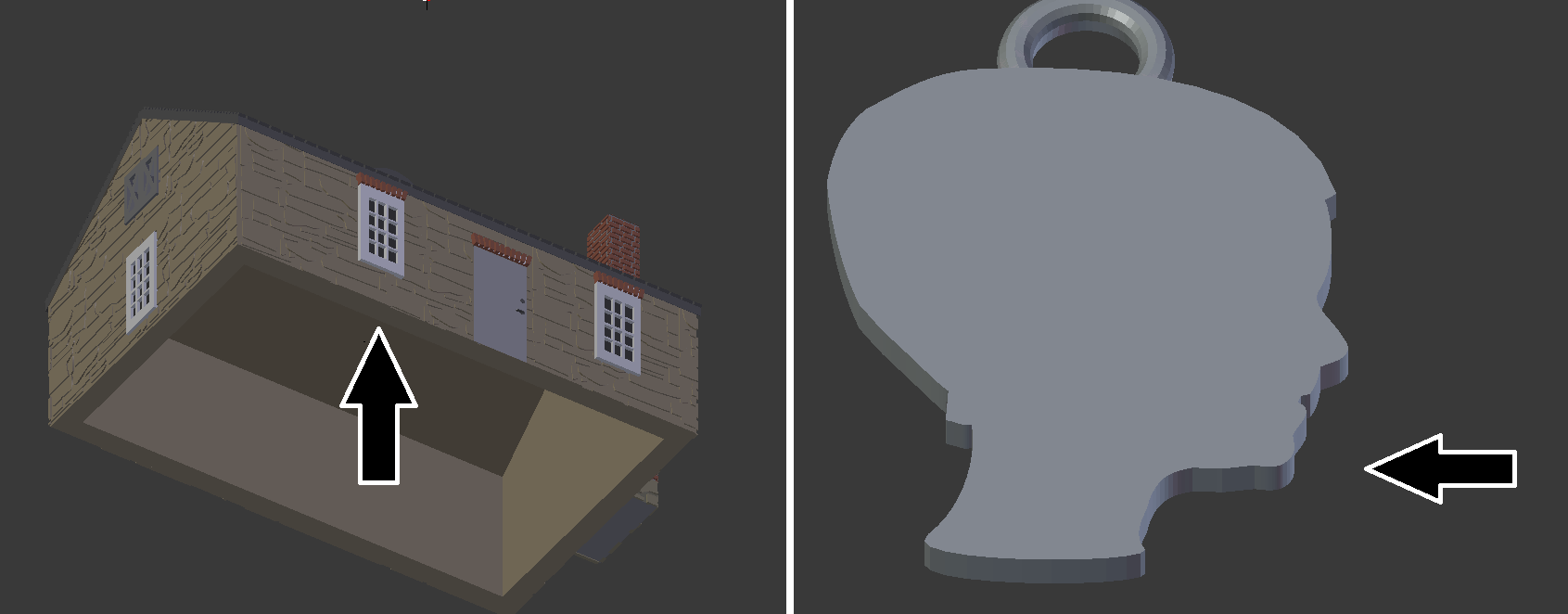
It is not a hard and fast rule, and you may fine-tune what works best with your printer. As a starting point for your design requirements, I tend to give supported walls at least 1mm in thickness and unsupported walls at least 2mm in thickness. For sections that I feel may need extra strength, I consider sizing those portions up to 3-5mm.
Other considerations – flat bases
With FFF/FDM printers, the printer starts with one initial layer which, if all goes well, sticks to the print bed for the duration of the print. If you have seen musings about hairspray, glue sticks, painter's tape, those are all measures to assist that important first layer in staying put. When you are designing for an FFF/FDM printer, it is ideal for the design to have a good footprint, a perfectly flat section to print straight on the print bed.
Sometimes a nice flat base isn’t going to be possible with the design you have in mind. The slicing software for the printer can assist in those cases. For designs that have small footprints that would not have a lot of contact area on the print bed, the slicer can add a temporary foundation printed underneath your object, a raft, to keep that all-important first layer stationary. If we did decide to print the coordinate bracelet on its side to take advantage of better detailing, the base of that print is just a very thin line, not likely to stay secure for the duration of the print. The raft, however, helps give it a sturdy anchor:
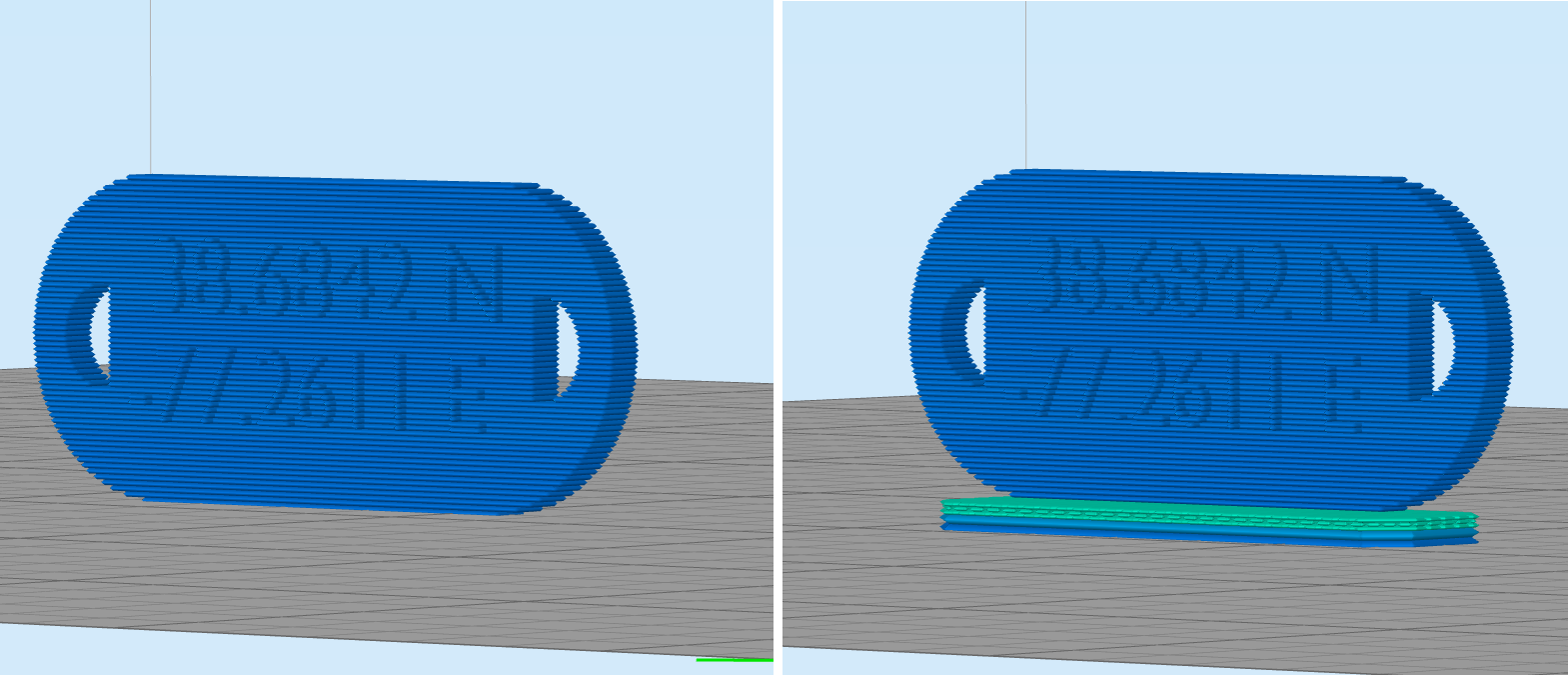
Home printing – Stereolithography (SLA) printers
Another printing technology that is becoming more accessible at home is the Stereolithography (SLA) printer, commonly referred to as Resin Printers. Instead of a spool of plastic filament, the raw material for resin printers is a pool of UV-sensitive liquid. The printer works by using a UV light to cure and solidify just the sections that will become your object. Your object is raised slightly out of the liquid pool, a process called peeling, and then the printer will solidify the next layer of your object and so on.
Overhangs
SLA printers tend to have a lot more flexibility with overhangs. The design guidelines for one of the most common desktop SLA printers, the Formlabs Form 2, support up to 71 degree overhangs, a substantial improvement over the FFF/FDM printers. SLA printers can also handle those small, completely horizontal overhangs for embossed detailing. The Form 2 Design Requirements refers to those as unsupported overhangs and recommends keeping them at a height of 1mm or less.
Detailing
The Formlabs Form 2 can work in layer heights as small as 0.025mm. Its equivalence to extrusion width or nozzle size would be the beam of light that is interacting with the liquid resin. In the case of the Form 2, that is 0.14mm. Combined, the Form 2 Design Requirements say the printer can support details as small as 0.1mm.
Wall thickness
Although the light beam is 0.14mm, the Form 2 Design Requirements do recommend a minimum supported wall thickness of 0.4mm and unsupported wall thickness of 0.6mm. Part of the recommendation is due to the peeling process. Smaller walls could warp as your print is pulled out of the pool of resin between layers.
Other considerations – drain holes
If you are hoping for a design to be hollow inside, you will want to include holes in your model to allow excess, uncured, liquid to drain.
Service Bureaus – Selective Laser Sintering (SLS) and more
The 3D Printing Service Bureaus open up a lot of doors in regards to what materials you can have your pieces produced in. You can have your jewelry designs cast in precious metals such as gold and platinum. You can have functional items, such as bottle openers, printed in sturdy stainless steel. You can have your custom designed coffee cup made in food-safe porcelain.
When working with at-home FFF/FDM printers, sometimes you have to put in the investment to learn your printer and its capabilities. At the 3D Printing Service Bureaus, they have already done that assessment for you and have documented design requirements for each material:
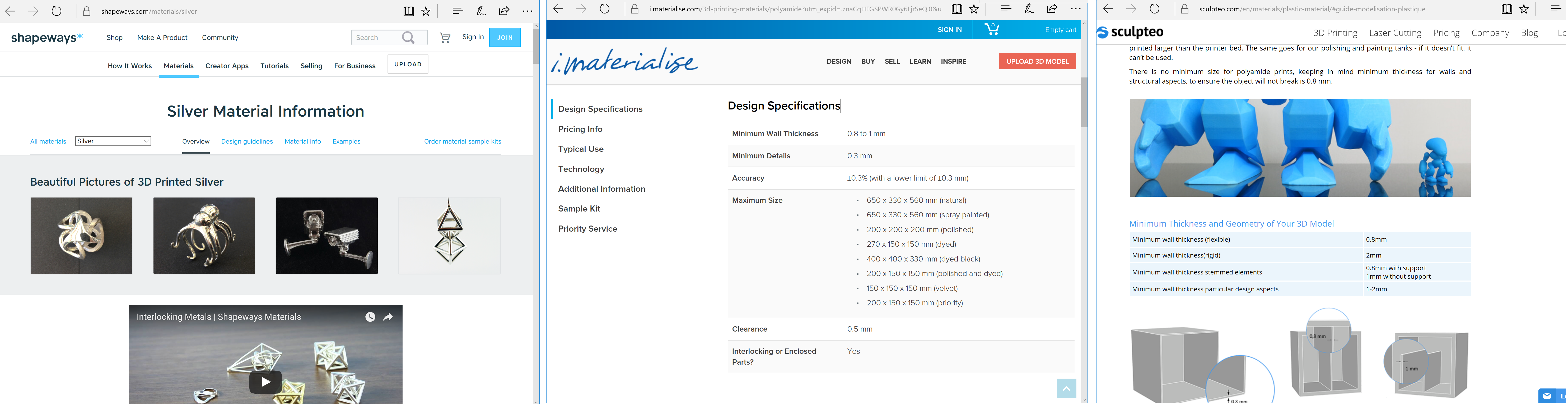
Overhangs
It can vary by material, but the printing processes at the large Service Bureaus often free you from the concern of overhangs. The industrial Selective Laser Sintering (SLS) printers used for Nylon pieces, for example, have an ingenious way to get around the gravity problem. The whole print bed is covered in a layer of nylon powder. A laser will heat up and solidify just the sections of powder that will become the first layer of your object. A fresh layer of powder is laid down on the printer and the laser will solidify the next layer of your object. The printing process finishes with a big block of powder on the printer. Your piece is dug out of the loose powder, much like an archaeologist excavating pottery from soil.
Because the excess powder provides a natural support system, even completely horizontal overhangs are achievable. You also don't have to worry about flat bases and having solid contact with the print bed. The extra powder from previous layers is there to act as a foundation no matter where or how small your object starts.
Details
Depending on the material and the process, the cutting edge printers at the 3D Printing Service Bureaus can offer up a higher level of detailing and resolution than your typical home printer. This will be specific to the material you select. High Definition Acrylate would permit embossed and engraved details as small as 0.1mm. Porcelain, on the other hand, has very different requirements. Porcelain pieces finish up with a glazing process. Since the glaze adds its own thickness to the piece, it could pool into crevasses and obscure shallow details. As a result, a model geared for porcelain would need to have much deeper engravings, at least 1mm.
The section name could vary in the Design Requirements or Material Information Sheets. Examples from three 3D Printing Service Bureaus are shown as follows:
Service Bureau | Section(s) |
iMaterialise | Minimum Details |
Sculpteo | Minimum width and height details |
Shapeways | Minimum Embossed Detail, Minimum Engraved Detail |
Wall thickness
The 3D Printing Service Bureaus offer a lot of perks with top-notch quality. Their services are, as expected, more expensive than a print from a desktop FFF/FDM printer. Part of the cost is determined by the amount of material you use. This could be expensive, particularly in the case of pricey cast metals such as platinum or gold. As you design for one of the Service Bureaus, you'll likely want to minimize the amount of material being used to keep your cost low. Suddenly the minimum wall thickness takes on a deeper meaning. To save cost, you may opt to make your object hollow. You may also opt to make your walls as thin as possible.
How thin can your piece be? Look for sections mentioning "wall thickness." Examples for three 3D Printing Service Bureaus are shown as follows:
Service Bureau | Section(s) |
iMaterialise | Minimum Wall Thickness |
Sculpteo | Minimum wall thickness (flexible), Minimum wall thickness (rigid) |
Shapeways | Min supported wall thickness, Min unsupported wall thickness |
Other considerations – escape holes
Since the SLS printing process creates a big block of powder, you will want to keep in mind how that powder will be cleaned out of your piece. If you intend for your piece to be hollow inside, for example, you will need to include an escape hole in your piece to allow the technicians to remove excess powder.
Comparing the Requirements
Although there additional printing processes, such as Binder Jetting, we don't have to discuss them all to understand how the process and the material can impact your design. Your decisions about overhangs, detail size, and wall thicknesses all vary with the final material and process. To serve as some starting guidelines, a summary of the three processes we did discuss are:
Design requirement | FFF/FDM (0.4mm Nozzle) |
SLA (Form2 at 0.10 Layers) |
SLS (Shapeways Strong & Flexible Plastic) |
Minimum supported wall thickness | 1mm | 0.4mm | 0.7mm |
Unsupported wall thickness | 2mm | 0.6mm | 0.7mm |
Overhangs | 45 degrees or less | 71 degrees or less | Any |
Height of unsupported overhangs | 0.5mm | 1mm | Any |
Minimum detail (vertical faces) | Layer height | 0.1mm | 0.2mm |
Minimum detail (horizontal faces) | Extrusion width | 0.1mm | 0.2mm |
Other | Flat base recommended | Drain holes may be needed | Escape holes may be needed |
Even when you decide on how you'll print your design, there are still some questions worth reflecting on. For example, how big do you want your print to be?
Thinking about size
Once you have an idea of which printing process will be used, I recommend thinking about the final size of your piece. We've put some thought into how high we want to emboss detailing as well as our wall thicknesses. If we made our entire model without thinking of the final dimensions, we would have to resize everything accordingly at the end.
If I scaled my piece down, suddenly I may have walls that are too thin to pass the automated checks at one of the 3D Printing Service Bureaus. Or perhaps I scaled my final piece up, making all my vertical detailing too large for an FFF/FDM printer to make without adding extra supports. You always have the ability to edit your model and there is indeed a natural iterative process to design. However, mass changing dimensions can be tedious and time consuming, possibly demoralizing. It is well worth a few moments to get out a tape measure or calipers and reflect on sizing.
Sizing for the printer
Regardless of the type of printer being used, it will have some size limitations. With the home FFF/FDM or SLA printers, you may be mainly concerned about the size of your print bed. With the 3D Printing Service Bureaus, economic forces may have you more concerned by cost. Some 3D Printing Service Bureaus will also have a minimum size requirement as well. If you do wish to push the limits in either direction, the technical specifications of the printer or the Material Design Requirements will guide you accordingly.
If your design is too big, don’t abandon it just yet. First off, if it is slightly too big for your print bed, remember that the hypotenuse of a triangle is longer than the other sides. See if placing your object at a diagonal will give you the room you need. Your print bed may only be 200mm x 200mm, but the diagonal could accommodate almost 283mm. If all else fails, you can split your model into parts to be printed separately.
Sizing for function
The function of what you are designing could go a long way to determining the size. This is particularly true if you are combining your print with another part. If I had a lobster claw clasp I wanted to use with a custom designed pendant, I would want to make sure the hook for that pendant was wide enough for the clasp. Once that is decided, aesthetics may kick in. I may size the rest of the piece purely to look proportionate with the hook.
Existing objects also give good direction with sizing. Making a coaster? Measure a coaster you already have. Holiday ornaments, paperweights, bottle openers, magnets, soap dishes, earrings, bookmarks, and business card holders are just the tip of the iceberg. Your house and your office are full of reference objects to guide you with sizing.
Sizing for yourself
Finally, when designing jewelry or accessories, it makes sense to take the tape measure to yourself. Get a feel for what would look good on you and what would look too clunky. Use your own dimensions to guide the dimensions of your 3D model.
Sometimes online references can help you with jewelry and accessory sizing. For example, if you are making a ring and know the ring size, there are conversion charts to translate the ring size to the inner diameter in millimeters.
Summary
In this chapter, you learned to think about the printing process and how each approach impacts your overhangs, your detail size, and your wall thicknesses. You also learned to think ahead about sizing so you can model your object to the desired size from the very beginning.
In the Chapter 2, Using a Background Image and Bezier Curves, you will start to make a custom profile pendant in Blender for 3D printing.